Куда приводит дао «Тойоты»?
Как алтайское предприятие с помощью кайдзен увеличило производство в 4 раза19.12.2016
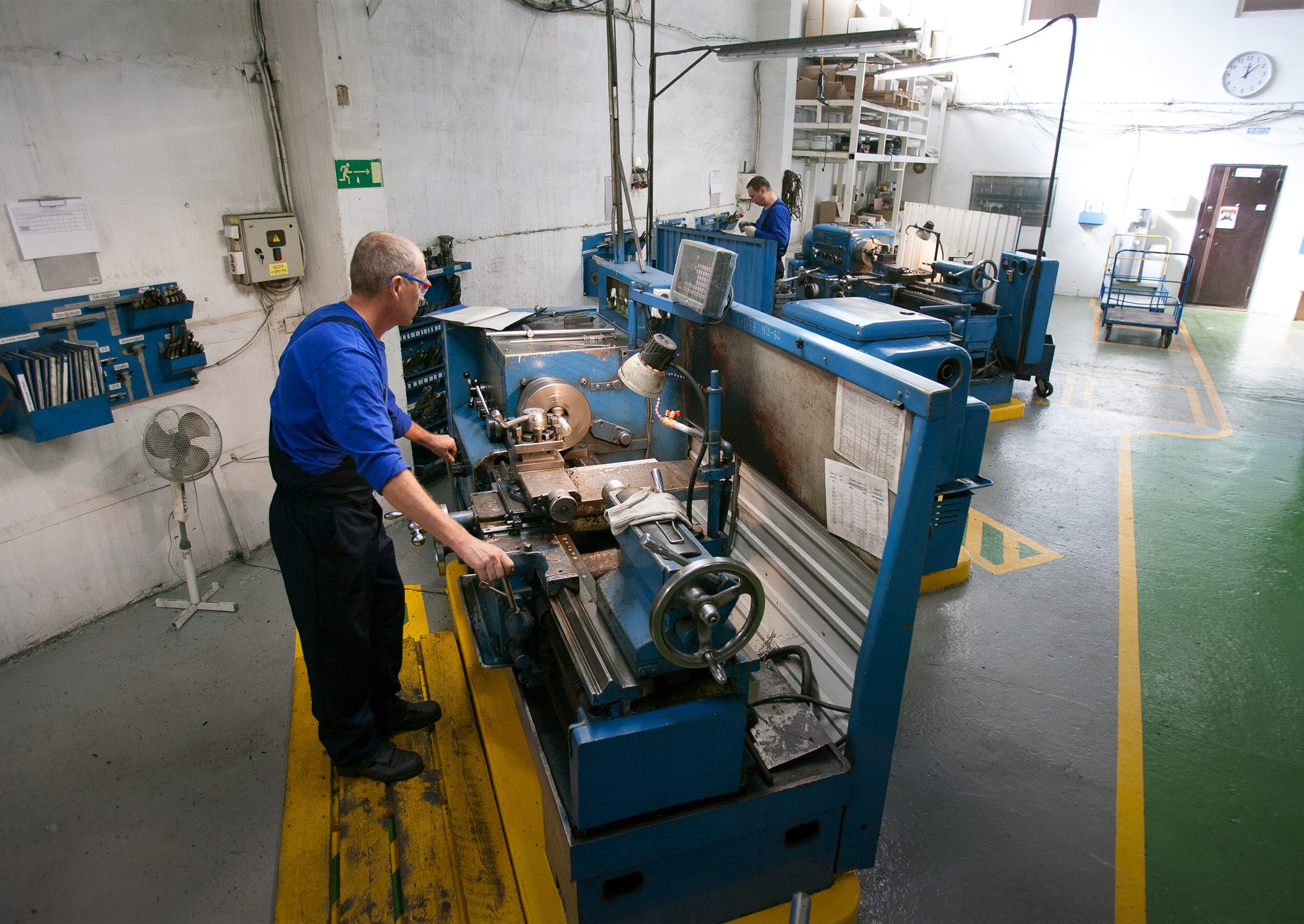
Алтайская компания «АлтайСтройМаш», специализирующаяся на производстве оборудования для газобетона, – одно из немногих предприятий в Сибири, на котором стали использовать технологию «бережливого производства», разработанную в японском автоконцерне Toyota. Японская идеология «кайдзен» на алтайской земле принесла свои плоды. Предприятию удалось вчетверо увеличить мощность производства, сократить издержки и повысить интенсивность использования оборудования. «Жажда» разбиралась в предпосылках внедрения кайдзен и в том, как работает методика на сибирском предприятии.
Работать быстрее и легче
К тому моменту г-н Бурдовицын был хорошо подкован теоретически. Как утверждает собеседник, он прочитал десяток книг по бережливому производству и три года пытался внедрить японские методики на своем заводе. Однако получалось не все.
Что происходило на производстве? Работа шла, но на результат влияли многие внутренние проблемы. По словам нашего собеседника, если сварщик делал кривой шов, то сборщики над ним шутили, но деталь принимали. Один бросал в угол металлический лом – остальные повторяли за ним. Когда приходил заказ на линию, все могло быть готово, кроме мелкой детали. Ждали, пока ее изготовят, 7-10 дней. Погрузить готовую линию в машину рабочие шли вдвоем – один должен был принимать груз в кузове.
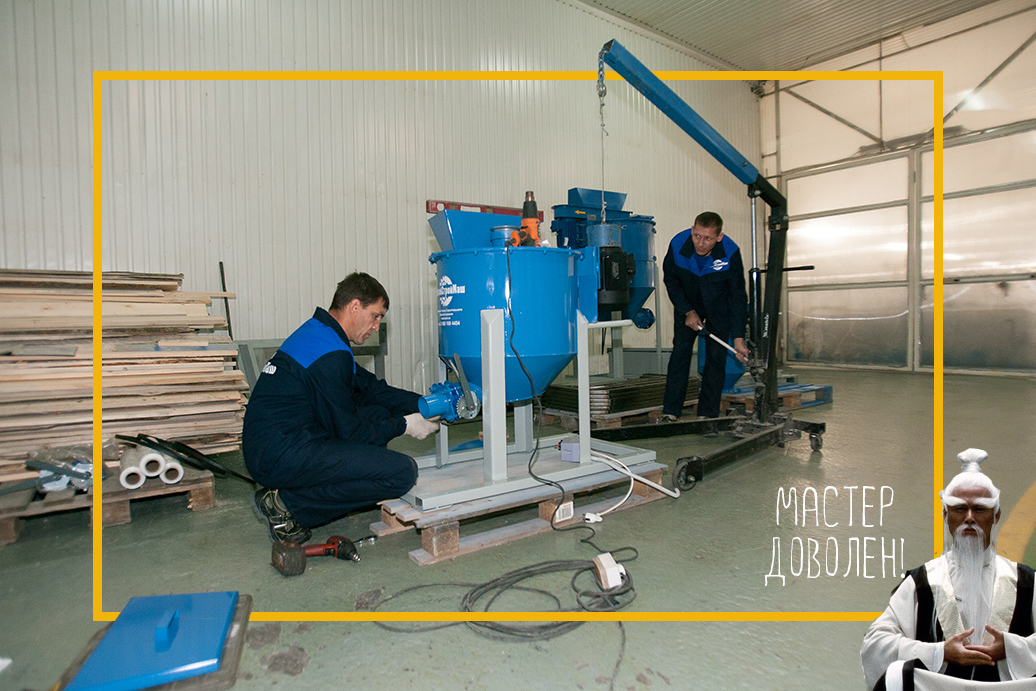
Все это тормозило и утяжеляло производство. Каждый заказ клиенты ждали по 2-3 недели – только к отгрузке. Дальше еще предстояла доставка. Так собиралась очередь, в которой не все были готовы ждать.
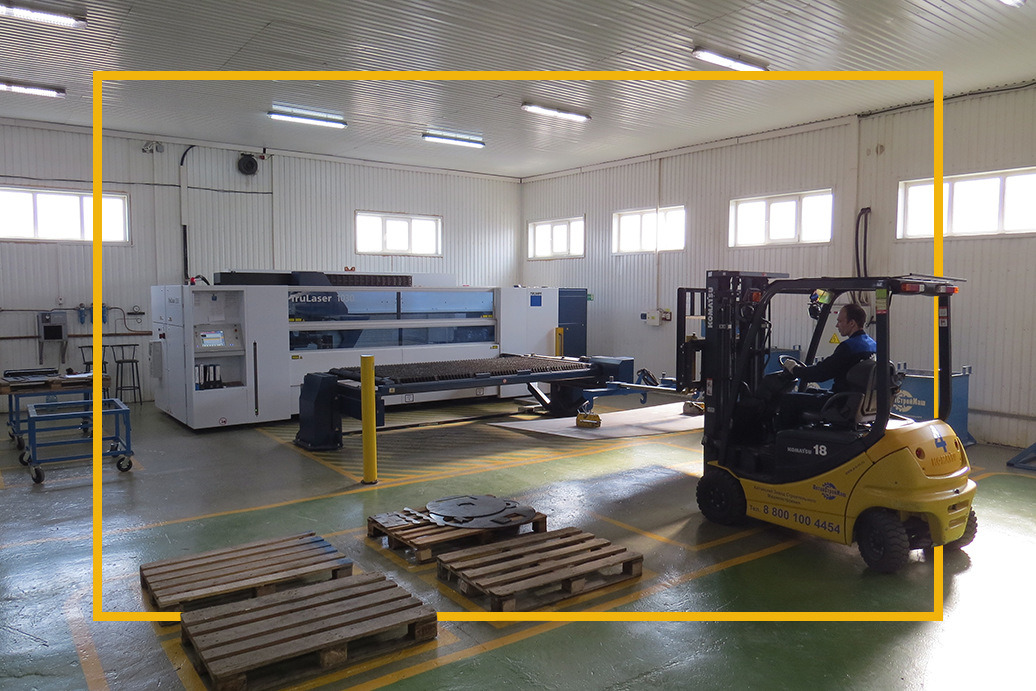
Поразила простота
Алексей Бурдовицын: «Во время экскурсии по заводу Toyota и общения с японскими специалистами меня удивили не какие-то новые «секретные» знания. Поразила простота процессов и действий персонала. Со стороны казалось, что рабочим легко – они действуют быстро и технично, как будто сами выпущены с конвейера «Тойоты». В каждом цехе чисто, и это выглядит естественно – ни одного источника привычной заводской грязи».
По словам нашего собеседника, работа идет последовательно – сколько деталей заказано, столько и произведено. Нет промежуточных складов и ничего не хранится «на будущее». Место каждого инструмента подписано и пронумеровано. Не потому что рабочие не отличают ключ от отвертки, а для эргономики. Запомнил место инструмента – в следующий раз нашел быстрее и вернул туда же.
Изменения на производстве в «АлтайСтройМаше» внедряли сразу после первой поездки в Японию – в 2013 году. Тогда же г-ну Бурдовицыну стало ясно, что было не так в 2010, когда началось заочное знакомство с бережливым производством.
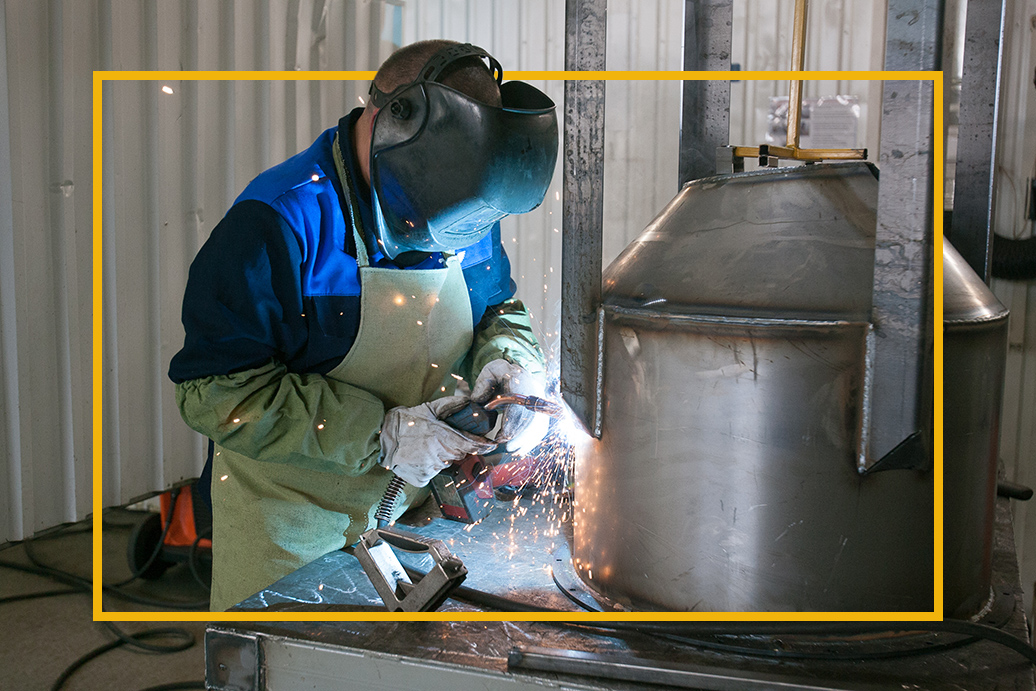
Постепенно на предприятии нашли оптимальное место у каждого станка и сделали разметку на полу – чтобы не теряться в пространстве. Вывезли тонны лишнего железа и поставили большие контейнеры в цехах. Закрепили на стенах панели для инструментов – чтобы ничего лишнего не лежало на станках. Рабочим понравилось. Раньше им просто некуда было убирать инструмент, если нужно держать его под рукой.
Четко определились с браком. Если деталь не соответствует стандарту – не передаем ее дальше и не принимаем к работе.
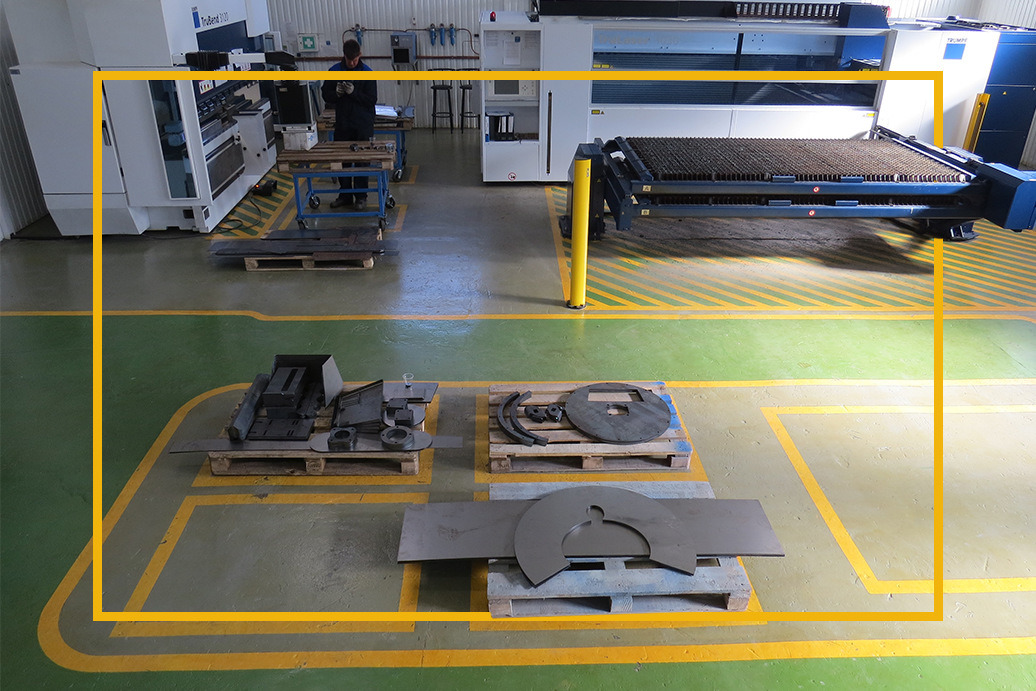
Увеличили, снижая
Суть бережливого производства – в снижении потерь. Поэтому главными маркерами успеха было – сколько времени, денег и сил стал экономить «АлтайСтройМаш».
Измерить затраты на внедрение бережливого производства в деньгах довольно сложно, и наш собеседник затрудняется привести конкретные суммы. Большей частью было затрачено время руководителей и сотрудников.
Впрочем, результаты внедрения выглядят впечатляюще. Мощность производства увеличилась почти в 4 раза – с 270 комплектов оборудования в год до 1000. Раньше многие клиенты не готовы были ждать 3-4 недели и уходили, сейчас они работают с «АлтайСтройМаш».
Снизилось количество складских запасов. Раньше предприятие закупало столько сырья, сколько поместится на складе. После введения бережливого производства – столько, сколько нужно на оплаченные заказы.
Кроме цифр, о результатах внедрения отлично рассказывает порядок. С началом внедрения принципов «Тойоты» стало больше экскурсий на завод. Водить клиентов по цехам приятно, и есть повод поддерживать чистоту, резюмирует собеседник.
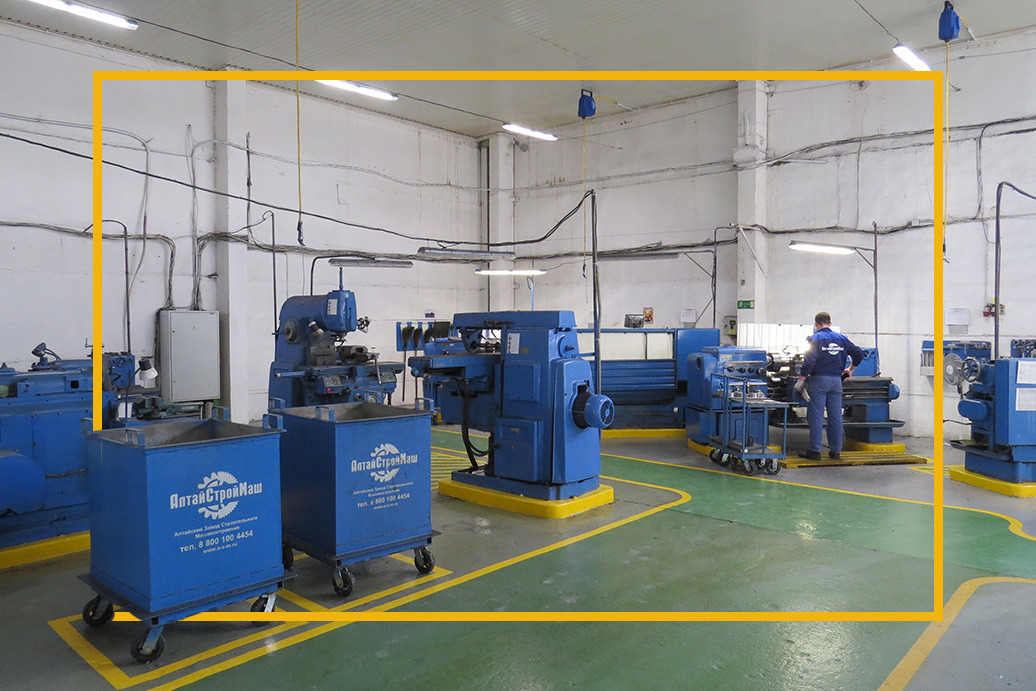
Бережливое производство «АлтайСтройМаш» в цифрах и фактах
Начало внедрения методики
2010 год. Интенсивно – с 2013 года.
Основные результаты:
– Увеличение мощности производства с 270 комплектов оборудования до 1000 в месяц.
– Снижение срока поставки с 3-4 недель до 3-4 дней.
– Полное отсутствие серийного брака.
– Снижение затрат на складские запасы в 10 раз: с 20 млн рублей до 2 млн рублей.
Сайт предприятия – http://www.asm.ru
Что такое система бережливого производства?
Бережливое производство (lean manufacturing (англ.) – стройное производство) – методика управления предприятием, предполагающая постоянное сокращение потерь.
Основной постулат системы – вовлечение в процесс улучшения и оптимизации бизнеса каждого сотрудника. Концепция бережливого производства стала развитием производственной концепции автоконцерна Toyota. Принципы после Второй Мировой войны сформулировал сотрудник корпорации Тайити Оно. Он классифицировал семь видов потерь, которые существуют на любом традиционном производстве, и наметил пути по их сокращению.
-
ААА
-
Сергей Марков